最新资讯
联系我们
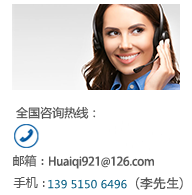
-
产品名称: 思瀚发布《中国铜球行业市场调查与研究及发展前途投资可行性研究报告
-
产品类型: 着色氧化
-
来源: mile米乐体育平台
-
发布时间: 2024-11-13 18:11:29
- 产品描述
-
铜球是一种电镀材料,下游应用领域最重要的包含 PCB 制造、光伏电池板制造、五金电镀等,其中铜球实现的基本功能都是在铜电镀过程中作为阳极材料向镀液中补充铜离子
铜球产品(以磷铜球为主)是铜电镀工序的主要物料,铜球的品质对镀层的品质和制造良品率具备极其重大的影响。随技术的慢慢的提升,主流阳极电镀铜材料完成了由从纯铜材料向添加了磷元素的磷铜合金材料转变,发展过程如下:
硫酸盐镀铜是应用最广泛的无氰镀铜工艺,具有成分简单,成本低,维护方便等优点,加入添加剂后,可直接获得光亮镀铜层,从而省去了机械抛光工序。
在 1954 年以前,硫酸盐镀铜工艺中采用的是纯铜作为阳极,由于电镀液中含有硫酸,使得纯铜阳极在电镀液中溶解很快,导致电镀液中的铜离子迅速累积,失衡。另一方面纯铜阳极在溶解时会产生少量一价铜离子(Cu+),它在电镀液中很不稳定,通过歧化反应分解成为二价铜离子(Cu2+)和微粒金属铜,在电镀过程中很容易在镀层上面成为毛刺。
为消除阳极Cu+的影响,人们最早使用阳极袋,但泥渣过多妨碍了电镀液的循环。后改用无氧高导电性铜阳极,虽然泥渣减少了,但仍不能阻止铜金属微粒的产生,于是又采用定期在电镀液中加入双氧水使Cu+氧化成Cu2+,但此法在化学反应中要消耗一部分硫酸,导致电镀液中的硫酸浓度下降,必须及时补充,同时又要补充被双氧水氧化而损耗的光亮剂,增加了电镀成本。
1954 年美国 Nevers等人对铜阳极的研究发现在铜阳极中渗入少量的磷,经过一段时间的电解处理后,铜阳极的表面生成一层黑色胶状的“磷膜”,它的主要成分是磷化铜(Cu3P,又称阳极膜),在电镀时阳极溶解几乎不产生铜粉,泥渣极少,零件表面铜镀层不会产生毛刺。这是由于含磷铜阳极的黑色膜具有导电性能,其孔隙又不影响铜离子自由通过,加快了 Cu+的氧化,阻止了 Cu+的积累,大大地减少了电镀液中 Cu+;同时又使阳极的溶解与阴极沉积的效率渐趋接近,保持了镀铜液中铜含量平衡。
美国福特汽车公司使用这种含磷铜阳极的经验证明既保证了镀铜层质量,又大幅度降低了电镀光亮剂的消耗,降低了成本。从此以后,含磷铜阳极在酸性镀铜行业中被广泛采用,随后又逐渐被 PCB行业大规模使用。
含磷铜阳极这一成果为硫酸盐光亮镀铜工艺的发展做出了重大贡献。在电镀的生产的全部过程中,“磷”的加入有两个功能:一是为了抑制Cu+的产生;二是阻止 Cu+进入溶液,促使它进一步被氧化成Cu2+。“磷”在理论上亦为杂质,在满足以上两个功能的基础上,添加得越少越好。早期,由于设备差、技术水平不高,搅拌难以充分,不能确保磷分布均匀,只好采取加大磷含量的措施,通常将磷含量控制在 0.1%~0.3%。到二十世纪 70~80 年代,国外采用电解铜(或无氧铜)和磷铜合金为原料,用中频电炉熔炼,磷含量容易控制,逐渐形成了含磷量为 0.035%~0.070%的标准。
电子信息行业逐渐向精密化、集成化发展,要求铜球的晶粒尺寸要细小均匀,同时磷含量分布均匀,以保证阳极膜均匀,以此来实现在相同电流和酸性环境条件下,Cu2+的电离以及结合均匀,形成均一的镀膜。下业的发展和技术进步推动了铜球行业生产的基本工艺一直在改进,技术标准逐步的提升,产品向微晶化、低磷化的方向发展。
目前,PCB 制造是铜球的最主要应用领域,也是对铜球产品技术方面的要求最高的领域,PCB 行业较为成熟,公开的行业数据较为多,以 PCB 行业有关数据计算 PCB 制造用铜球市场空间如下:根据 Prismark 数据,铜球约占 PCB 成本的6%;2023 年全球 PCB 产值为 695.17 亿美元,国内 PCB 产值为 377.94 亿美元。
据此测算,2023 年全球铜球市场规模约为人民币 235.14 亿元,国内铜球市场规模约人民币 127.84 亿元。未来,随着终端应用的不断加深以及行业整体规模的提升,铜球产品的市场规模亦会不断增长。
印刷电路板,即 Printed Circuit Board,简称 PCB,是一种重要的电子器件,是电子元器件的支撑体,也是电子元器件电气相互连接的载体。PCB 是组装电子零件用的关键互连件,不仅为电子元器件提供电气连接,也承载着电子设备数字及模拟信号传输、电源供给和射频微波信号发射与接收等功能,绝大多数电子设备及产品均需配备,因而 PCB 也被称为“电子科技类产品之母”,被普遍的应用于通信、计算机、消费电子、汽车电子、工业控制和医疗、航空航天等行业。
PCB 的制造品质不仅直接影响电子科技类产品的可靠性,而且影响芯片与芯片之间信号传输的完整性,其产业的发展水平可在某些特定的程度上反映一个国家或地区电子信息产业的发展速度与技术水平。
PCB 上游生产原材料最重要的包含覆铜板(CCL)、铜箔、铜球/氧化铜粉、油墨、金盐及其他化工材料。其中,铜球(一般都会采用磷铜球)主要在 PCB 电镀工序中作为阳极氧化,参与化学反应,铜球约占 PCB 成本的 6%。PCB 应用场景范围广泛,下游应用涵盖通信、计算机、消费电子、汽车电子、工业控制和医疗、航空航天等领域。
随着电子技术的提升及电子科技类产品的快速更迭,全球 PCB 产业呈现持续增长的发展的新趋势。根据 Prismark 数据,2022 年度全球 PCB 产值达到 817.4 亿美元,2010-2022 年,全球 PCB 产值复合增长率达到 3.8%。预计 2028 年全球 PCB 产值在通信和消费电子领域的带动下将增长至 904.1 亿美元,2023-2028 年复合增长率为 5.4%。全球 PCB 行业市场需求将逐步扩大,各大 PCB 制造商未来的扩产计划及设备换新需求将极大推动 PCB 产业链的慢慢的提升和发展。
根据 Prismark 及公开资料,全球 PCB 行业于过去几十年中经历了多次产业格局变化。二十世纪 80 年代,美国作为全球 PCB 技术的主导国家,其 PCB 产值占全球总产值比例超过 30%;90 年代后,日本企业突破了 PCB 制造技术,超越美国成为新的制造中心;2000 年之后,中国台湾 PCB 市场迅速崛起,而欧美国家及日本迫于成本压力则相应收缩其 PCB 产值;自 2005 年以来,中国大陆依靠较低的综合成本、庞大的市场需求、逐步完善的配套资源等优势,成功超越日本并于当年首次成为全世界最大 PCB 生产制造中心。
中国大陆 PCB 产值全球占比逐步由 2000 年的 8.1%,增加至 2008 年的 31.0%,进而增加至 2022 年的 53.3%。PCB 产业格局东移明显,过去二十多年来中国大陆 PCB 产值全球占比不断的提高,预计未来几年仍将保持领先,占据世界核心地位。从 PCB 行业的发展来看,中国大陆虽然慢慢的变成了世界第一的 PCB 生产大国,但附加值较高的 PCB 产品的生产技术及市场份额,仍被欧美日等发达国家占据。
日本目前为全球最大的高附加值 PCB 生产地区,产品以多层板、HDI 板、IC 载板、FPC 为主;美国同样维持了高附加值 PCB 的研发及生产职能,产品以高阶、多层板为主,主要应用领域包括通信、医疗、航空航天、军工等领域。
从 PCB 产品结构情况来看,PCB 市场刚性板仍占主流地位,其中多层板是全球 PCB 行业中产值最大的产品;伴随 5G 基站、数据中心和网络技术设施设备、消费电子类可穿戴设备、IoT 市场等下游领域的快速发展,HDI 板、IC 载板及 FPC 等高附加值的 PCB 产品呈现迅速增长态势,预计未来几年也将保持较高的发展增速。
据 Prismark 预计,2023 年 HDI 线 亿美元,受库存改善和对汽车、高速光模块(400G、800G)、卫星通信和人工智能边缘设备的需求扩大的推动,全球 HDI 线 年 CAGR 将达 7.1%。
2023 年全球 IC 封装基板市场规模达 125.0 亿美元,受 FCBGA 用于高级 2.5 和 3D 封装领域、新兴的 AiP 和 SiP 基板及 FCCSP和存储器基板的持续增长等因素影响,预计 2028 年全球 IC 封装基板市场规模将达 190.7 亿美元,2023-2028 年 CAGR 达到 8.8%。两者年均复合增长率均超过行业整体增幅。
现阶段,高端 HDI 材料及封装基板材料主要集中于中国台湾、日本、韩国企业。随着国内厂商技术创新并进入核心供应链,预计未来几年中国大陆地区企业在 HDI 和 IC 载板材料的行业产值占比将大幅提升。
按照下游应用领域分布来看,根据 Prismark 的统计数据,2022 年度,计算机和通信为 PCB 的主要应用市场,应用占比分别为 33%和 32%。其次为消费电子、汽车电子领域,应用占比分别为 14%和 12%。其它领域,如工控医疗、军事/航空航天等应用占比相对较低。
我国 PCB 行业的整体发展趋势与全球 PCB 行业基本相同。受益于 PCB 行业产能不断向我国转移,加之通信、计算机、消费电子、汽车电子、工业控制和医疗、航空航天等下游领域的需求增长刺激,近年来我国 PCB 行业增速整体高于全球 PCB 行业增速。
根据 Prismark 数据,中国作为全世界最大的 PCB 生产基地,2022 年度 PCB 产值达到 435.5 亿美元,2010-2022 年,中国 PCB 产值复合增长率达到 6.6%,增速超过全球增速平均水平;预计 2028 年中国 PCB 产值将增长至 464.7 亿美元,2023-2028 年复合增长率将达到 4.2%。中国 PCB 市场目前发展势态平稳,预计未来增速将与全球增速基本持平。
中国已形成了较为成熟的电子信息产业链,同时具备内需市场广阔、人力成本较低、投资环境良好等优势,吸引了大量外资企业将生产重心向中国大陆转移。珠三角地区、长三角地区由于下游产业集中,并具备良好的区位条件,成为了我国 PCB 生产的核心区域。但近年来,随着沿海地区制造成本上升,部分 PCB 企业开始将产能向中西部地区迁移,尤其是江西、湖北、重庆等经济产
业带的 PCB 产能呈现快速增长的发展势头。江西省作为沿海地区向中部延伸的重要地带,兼具独特的地理位置及丰富的资源优势,加上地方政府大力支持电子信息产业发展,逐渐成为沿海地区 PCB 企业主要转移基地。预计未来珠三角地区、长三角地区仍将保持 PCB 产业的领先地位,并不断向高端产品和高附加值产品方向发展;中西部地区由于 PCB 企业的内迁,逐渐成为我国 PCB 行业的重要生产基地。
随着全球产业规模的不断扩张,中国区域的 PCB 产业也呈现持续升级的发展态势,高阶多层板、FPC、HDI 板等产品的产能均得到一定提升。
PCB 细分产品中,多层板产值占比最高,其次是单/双面板、HDI 板和 FPC,IC 载板占比稳步提升。和全球 PCB 市场产品结构对比来看,中国市场的单/双面板和多层板的规模占比高于全球市场,而 IC 载板和 FPC 的规模占比低于全球市场,可见在附加值较高的 PCB 产品的生产技术及市场份额等方面,中国尚不及欧美日等发达国家。
随着技术的迭代和产品应用的升级,国内主要 PCB 厂商也不断向高阶产品进发,在HDI 板、IC 载板和 FPC等领域不断扩大产能,随着高阶 PCB 产品的持续布局,未来中国厂商将凭借成本、效率等优势逐步抢占高阶 PCB 的市场份额。
按照下游应用领域分布来看,根据世界电子电路理事会(WECC)数据,2022 年中国 PCB 行业下游应用领域中,通信、计算机、汽车电子和消费电子合计占比 87%,是最主要的四大应用市场。
在通信领域,PCB 主要运用于通信基站、传输设备、路由器、交换机、服务/存储设备等。2020 年是全球 5G 规模扩展元年,各国纷纷加快 5G 建设。5G对通信设备性能要求提升导致单体基站 PCB 量价齐升,以及 5G 基站的换建与新建,使得 PCB 在通信领域将迎来高速成长期。在计算机领域,PCB 主要运用在服务器/存储器、个人电脑及外部设备等设备中。
近年来,随着云计算、大数据等技术发展,互联网数据中心作为处理、存储、备份数据的重要物理载体快速发展,而云计算集中化和价格下降也倒逼互联网数据中心朝着大规模/超大规模发展,拉动了互联网数据中心的建设需求,同时带动了服务器和存储器的增长,使得计算机领域的 PCB 需求将大幅增加。
在汽车电子领域,PCB 主要运用于汽车电子控制装置(如发动机电子、底盘电子、驾驶辅助系统、车身电子)和车载电子装置(如娱乐系统)等。在智能驾驶和新能源汽车的驱动下,汽车电子单车配套价值的提升,汽车电子有望成为 PCB 发展的新动能。在消费电子领域,PCB 主要运用于手机、家电、可穿戴设备、无人机、VR/AR 设备等产品中。
消费电子种类多、更新快,叠加消费升级之大趋势,消费者逐渐从以往的物质型消费走向服务型、品质型消费。目前,消费电子行业正在酝酿下一个以人工智能、物联网、智能家居为代表的新蓝海,创新型消费电子产品层出不穷,并将渗透消费者生活的方方面面。
消费电子市场的快速增长也推动了 PCB 行业的发展。在工控医疗领域,PCB 主要运用于工业电脑、变频器、测量仪、医疗显示器等设备中。随着全球人口加速老龄化便携式医疗、家用医疗设备的需求急剧增长,使得医疗设备拥有广阔的发展前景。
随着电子技术的飞速发展,中国和全球 PCB 产业也在持续成长。根据Prismark 的数据,预计 2023-2028 年全球 PCB 产值在通信和消费电子领域的带动下将增长至 904.1 亿美元,复合增长率将达到 5.4%;中国 PCB 产值将增长至 464.7 亿美元,复合增长率将达到 4.2%。未来五年,中国和全球 PCB 市场将保持持续增长。
受益于全球 PCB 产能向中国转移以及下游蓬勃发展的电子终端产品制造的影响,中国已成为全球第一大 PCB 制造基地。根据 Prismark 预测,未来 5 年亚洲将继续主导全球 PCB 市场的发展,而中国在 PCB 行业的地位将更加稳固。
PCB 的下游终端应用领域广泛,包括通信、计算机、消费电子、汽车电子、工业控制和医疗、航空航天等。
广泛的终端应用分布为 PCB 行业提供巨大的市场空间,下游终端应用行业存量市场规模的稳定增长为 PCB 行业发展提供了基础,降低了行业发展的风险。同时,电子产业突飞猛进,下业技术不断革新,PCB 的下游终端应用市场呈现多元化趋势,产品的运用范围也大幅扩增,5G、Mini-LED、AR/VR、可折叠手机、新能源汽车等领域的蓬勃发展为 PCB行业带来了广阔的增量应用市场。
随着下游终端电子产品朝着高性能化、多功能化和信号传输高频(速)化的方向迅速发展,推动了 PCB 行业快速地从传统 PCB 走向以高集成化、高性能化为特点的高阶 PCB,具体体现如下:
(a)高系统集成化。智能终端的每次升级都会对产品的集成度和多功能化提出更高要求。以智能手机为例,在不断要求输入/输出端口数目增多、引脚间距减小、功能元件数增多的需求面前,PCB 产品设计日趋复杂,电路板上的集成密度不断提升。刚挠结合、埋入式元器件等小型化 PCB 产品能够提供更高密度的电路互连、容纳更多的电子元件,在多功能集成、体积重量减小等方面具有很大优势。全球主要 PCB 厂商均致力于在减小 PCB 产品体积与重量的同时附加更多的功能元件,这些要求对 PCB 电镀的精细度与信赖度提出更高的挑战。
(b)高性能化。高阶 PCB 产品未来将进入快速增长阶段,对数据传输频率及速度、数据容量的要求会更高。随着数字传输信号日益高频化,具备良好的阻抗性的 PCB 产品才能保障信息的有效传输。PCB 产品电路阻抗越低,其性能就越稳定,越可实现高频高速工作,从而承担更复杂的功能。PCB 产品高性能化的趋势也推动 PCB 的制作工艺向微孔化、细线化、多层化的方向发展。在此背景下,国内主要 PCB 厂商未来将致力于完善和扩充产品品类,不断提升高阶化 PCB 产品产能和产量。
凭借绿色、环保且成本持续下降等优势,近年来光伏行业处于快速发展阶段。为早日实现碳中和及碳达峰,我国政府积极推动光伏产业的健康发展,我国光伏新增装机量不断提升。根据中国光伏行业协会统计数据,2015 年我国光伏新增装机量为 15.1GWh,2022 年增长至 87.4GWh,年均复合增长率为 28.5%。
在我国光伏产业链成本日渐下降及产品技术持续提升的背景下,中国光伏行业协会预测,2023-2030 年我国年均新增光伏装机将达到 104-127GWh,全球光伏年均新增装机将达到 344-406GWh。
根据原材料和电池制备技术的不同,光伏电池可分为 P 型电池和 N 型电池。P 型硅片是在硅料中掺杂硼元素制成;N 型硅片是在硅材料中掺杂磷元素制成。2021 年后 N 型电池开始快速发展,其中以 TOPCon 和 HJT(异质结)两条路线为主导,两者现阶段处于大规模商业化的前期阶段。
TOPCon 和 HJT 电池技术理论光电转换效率超过 28%,具有非常大的市场潜力。根据中国光伏行业协会数据,2021 年全球光伏银浆消耗量约达 3,378 吨,耗银量占全球白银产量的 19%;2022 年我国光伏银浆消耗量预计 4,177 吨,同比增加 35.9%;浆料成本约占光伏电池成本的 10%~20%。
根据中国光伏行业协会《中国光伏产业发展路线 年)》,TOPCon 电池银浆消耗量约为 115mg/片,HJT 电池银浆消耗量约为 127mg/片,相比主流 PERC 技术银浆耗量 91mg/片,分别增加了 26.37%和 39.56%的银浆耗量。TOPCon、HJT 等 N 型电池技术的发展,光伏行业对银浆的耗用量会进一步增加。
电池片生产成本中的非硅材料具有很大的降本空间,其中,银浆的使用量大、价格高,银浆成本是非硅成本下降的关键。在不影响电池转化效率的前提下,可以减少贵金属银的使用量,利用价格较低的金属替代一部分银粉,从而达到降低成本的效果,具体操作方法包括铜电镀和银包铜。其中,铜电镀可实现铜替代银浆,并具有超细线宽、高可靠性、可量产性等优势。随着铜电镀等技术逐步成熟,光伏行业对铜球铜粉产品的需求将大大提升,铜球铜粉市场规模也将进一步扩大。
铜球是一种电镀材料,下游应用领域主要包括 PCB 制造、光伏电池板制造、五金电镀等,其中铜球实现的主要功能都是在铜电镀过程中作为阳极材料向镀液中补充铜离子。
铜球产品(以磷铜球为主)是铜电镀工序的主要物料,铜球的品质对镀层的品质和制造良品率具有重要的影响。随着技术的不断进步,主流阳极电镀铜材料完成了由从纯铜材料向添加了磷元素的磷铜合金材料转变,发展过程如下:
硫酸盐镀铜是应用最广泛的无氰镀铜工艺,具有成分简单,成本低,维护方便等优点,加入添加剂后,可直接获得光亮镀铜层,从而省去了机械抛光工序。
在 1954 年以前,硫酸盐镀铜工艺中采用的是纯铜作为阳极,由于电镀液中含有硫酸,使得纯铜阳极在电镀液中溶解很快,导致电镀液中的铜离子迅速累积,失去平衡。另一方面纯铜阳极在溶解时会产生少量一价铜离子(Cu+),它在电镀液中很不稳定,通过歧化反应分解成为二价铜离子(Cu2+)和微粒金属铜,在电镀过程中很容易在镀层上面成为毛刺。
为消除阳极Cu+的影响,人们最早使用阳极袋,但泥渣过多妨碍了电镀液的循环。后改用无氧高导电性铜阳极,虽然泥渣减少了,但仍不能阻止铜金属微粒的产生,于是又采用定期在电镀液中加入双氧水使Cu+氧化成Cu2+,但此法在化学反应中要消耗一部分硫酸,导致电镀液中的硫酸浓度下降,必须及时补充,同时又要补充被双氧水氧化而损耗的光亮剂,增加了电镀成本。
1954 年美国 Nevers等人对铜阳极的研究发现在铜阳极中渗入少量的磷,经过一定时间的电解处理后,铜阳极的表面生成一层黑色胶状的“磷膜”,它的主要成分是磷化铜(Cu3P,又称阳极膜),在电镀时阳极溶解几乎不产生铜粉,泥渣极少,零件表面铜镀层不会产生毛刺。这是由于含磷铜阳极的黑色膜具有导电性能,其孔隙又不影响铜离子自由通过,加快了 Cu+的氧化,阻止了 Cu+的积累,大大地减少了电镀液中 Cu+;同时又使阳极的溶解与阴极沉积的效率渐趋接近,保持了镀铜液中铜含量平衡。
美国福特汽车公司使用这种含磷铜阳极的经验证明既保证了镀铜层质量,又大幅降低了电镀光亮剂的消耗,降低了成本。从此以后,含磷铜阳极在酸性镀铜行业中被广泛采用,随后又逐渐被 PCB行业大规模使用。
含磷铜阳极这一成果为硫酸盐光亮镀铜工艺的发展做出了重大贡献。在电镀的生产过程中,“磷”的加入有两个功能:一是为了抑制Cu+的产生;二是阻止 Cu+进入溶液,促使它进一步被氧化成Cu2+。“磷”在理论上亦为杂质,在满足以上两个功能的基础上,添加得越少越好。早期,由于设备差、技术水平不高,搅拌难以充分,不能保证磷分布均匀,只好采取加大磷含量的措施,通常将磷含量控制在 0.1%~0.3%。到二十世纪 70~80 年代,国外采用电解铜(或无氧铜)和磷铜合金为原料,用中频电炉熔炼,磷含量容易控制,逐渐形成了含磷量为 0.035%~0.070%的标准。
电子信息行业逐渐向精密化、集成化发展,要求铜球的晶粒尺寸要细小均匀,同时磷含量分布均匀,以保证阳极膜均匀,从而实现在相同电流和酸性环境条件下,Cu2+的电离以及结合均匀,形成均一的镀膜。下业的发展和技术进步推动了铜球行业生产工艺不断改进,技术标准不断提高,产品向微晶化、低磷化的方向发展。
目前,PCB 制造是铜球的最主要应用领域,也是对铜球产品技术要求最高的领域,PCB 行业较为成熟,公开的行业数据较为多,以 PCB 行业相关数据计算 PCB 制造用铜球市场空间如下:根据 Prismark 数据,铜球约占 PCB 成本的6%;2023 年全球 PCB 产值为 695.17 亿美元,国内 PCB 产值为 377.94 亿美元。
据此测算,2023 年全球铜球市场规模约为人民币 235.14 亿元,国内铜球市场规模约人民币 127.84 亿元。未来,随着终端应用的不断加深以及行业整体规模的提升,铜球产品的市场规模亦会不断增长。
印刷电路板,即 Printed Circuit Board,简称 PCB,是一种重要的电子器件,是电子元器件的支撑体,也是电子元器件电气相互连接的载体。PCB 是组装电子零件用的关键互连件,不仅为电子元器件提供电气连接,也承载着电子设备数字及模拟信号传输、电源供给和射频微波信号发射与接收等功能,绝大多数电子设备及产品均需配备,因而 PCB 也被称为“电子产品之母”,被广泛运用于通信、计算机、消费电子、汽车电子、工业控制和医疗、航空航天等行业。
PCB 的制造品质不仅直接影响电子产品的可靠性,而且影响芯片与芯片之间信号传输的完整性,其产业的发展水平可在一定程度上反映一个国家或地区电子信息产业的发展速度与技术水平。
PCB 上游生产原材料主要包括覆铜板(CCL)、铜箔、铜球/氧化铜粉、油墨、金盐及其他化工材料。其中,铜球(一般采用磷铜球)主要在 PCB 电镀工序中作为阳极氧化,参与化学反应,铜球约占 PCB 成本的 6%。PCB 应用范围广泛,下游应用涵盖通信、计算机、消费电子、汽车电子、工业控制和医疗、航空航天等领域。
随着电子技术的提升及电子产品的快速更迭,全球 PCB 产业呈现持续增长的发展趋势。根据 Prismark 数据,2022 年度全球 PCB 产值达到 817.4 亿美元,2010-2022 年,全球 PCB 产值复合增长率达到 3.8%。预计 2028 年全球 PCB 产值在通信和消费电子领域的带动下将增长至 904.1 亿美元,2023-2028 年复合增长率为 5.4%。全球 PCB 行业市场需求将进一步扩大,各大 PCB 制造商未来的扩产计划及设备换新需求将极大推动 PCB 产业链的不断进步和发展。
根据 Prismark 及公开资料,全球 PCB 行业于过去几十年中经历了多次产业格局变化。二十世纪 80 年代,美国作为全球 PCB 技术的主导国家,其 PCB 产值占全球总产值比例超过 30%;90 年代后,日本企业突破了 PCB 制造技术,超越美国成为新的制造中心;2000 年之后,中国台湾 PCB 市场迅速崛起,而欧美国家及日本迫于成本压力则相应收缩其 PCB 产值;自 2005 年以来,中国大陆依靠较低的综合成本、庞大的市场需求、逐步完善的配套资源等优势,成功超越日本并于当年首次成为全球最大 PCB 生产制造中心。
中国大陆 PCB 产值全球占比逐步由 2000 年的 8.1%,增加至 2008 年的 31.0%,进而增加至 2022 年的 53.3%。PCB 产业格局东移明显,过去二十多年来中国大陆 PCB 产值全球占比不断提升,预计未来几年仍将保持领先,占据世界核心地位。从 PCB 行业的发展来看,中国大陆虽然已经变成全球第一的 PCB 生产大国,但附加值较高的 PCB 产品的生产技术及市场占有率,仍被欧美日等发达国家占据。
日本目前为全球最大的高的附加价值 PCB 生产地区,产品以多层板、HDI 板、IC 载板、FPC 为主;美国同样维持了高的附加价值 PCB 的研发及生产职能,产品以高阶、多层板为主,主要应用领域包括通信、医疗、航空航天、军工等领域。
从 PCB 产品结构情况去看,PCB 市场刚性板仍占主流地位,其中多层板是全球 PCB 行业中产值最大的产品;伴随 5G 基站、数据中心和网络技术设施设备、消费电子类可穿戴设备、IoT 市场等下游领域的加快速度进行发展,HDI 板、IC 载板及 FPC 等高的附加价值的 PCB 产品呈现迅速增长态势,预计未来几年也将保持比较高的发展增速。
据 Prismark 预计,2023 年 HDI 线 亿美元,受库存改善和对汽车、高速光模块(400G、800G)、卫星通信和人工智能边缘设备的需求扩大的推动,全球 HDI 线 年 CAGR 将达 7.1%。
2023 年全球 IC 封装基板市场规模达 125.0 亿美元,受 FCBGA 用于高级 2.5 和 3D 封装领域、新兴的 AiP 和 SiP 基板及 FCCSP和存储器基板的持续增长等因素影响,预计 2028 年全球 IC 封装基板市场规模将达 190.7 亿美元,2023-2028 年 CAGR 达到 8.8%。两者年均复合增长率均超过行业整体增幅。
现阶段,高端 HDI 材料及封装基板材料主要集中于中国台湾、日本、韩国企业。随着国内厂商技术创新并进入核心供应链,预计未来几年中国大陆地区企业在 HDI 和 IC 载板材料的行业产值占比将大幅提升。
按照下游应用领域分布来看,根据 Prismark 的统计数据,2022 年度,计算机和通信为 PCB 的主要应用市场,应用占比分别为 33%和 32%。其次为消费电子、汽车电子领域,应用占比分别为 14%和 12%。其它领域,如工控医疗、军事/航空航天等应用占比相对较低。
我国 PCB 行业的整体发展的新趋势与全球 PCB 行业基本相同。受益于 PCB 行业产能不断向我国转移,加之通信、计算机、消费电子、汽车电子、工业控制和医疗、航空航天等下游领域的需求量开始上涨刺激,近年来我国 PCB 行业增速整体高于全球 PCB 行业增速。
根据 Prismark 数据,中国作为全世界最大的 PCB 生产基地,2022 年度 PCB 产值达到 435.5 亿美元,2010-2022 年,中国 PCB 产值复合增长率达到 6.6%,增速超过全球增速中等水准;预计 2028 年中国 PCB 产值将增长至 464.7 亿美元,2023-2028 年复合增长率将达到 4.2%。中国 PCB 市场目前发展势态平稳,预计未来增速将与全球增速基本持平。
中国已形成了较为成熟的电子信息产业链,同时具备内需市场广阔、人力成本较低、投资环境良好等优势,吸引了大量外资企业将生产重心向中国大陆转移。珠三角地区、长三角地区由于下游产业集中,并具备良好的区位条件,成为了我国 PCB 生产的核心区域。但近年来,随着沿海地区制造成本上升,部分 PCB 公司开始将产能向中西部地区迁移,尤其是江西、湖北、重庆等经济产
业带的 PCB 产能呈现迅速增加的发展势头。江西省作为沿海地区向中部延伸的重要地带,兼具独特的地理位置及丰富的资源优势,加上地方政府全力支持电子信息产业高质量发展,慢慢的变成为沿海地区 PCB 企业主要转移基地。预计未来珠三角地区、长三角地区仍将保持 PCB 产业的领头羊,并不断向高端产品和高的附加价值产品方向发展;中西部地区由于 PCB 企业的内迁,慢慢的变成为我国 PCB 行业的重要生产基地。
随着全球产业规模的不断扩张,中国区域的 PCB 产业也呈现持续升级的发展态势,高阶多层板、FPC、HDI 板等产品的产能均得到一定提升。
PCB 细分产品中,多层板产值占比最高,其次是单/双面板、HDI 板和 FPC,IC 载板占比稳步提升。和全球 PCB 市场产品结构对比来看,中国市场的单/双面板和多层板的规模占比高于全球市场,而 IC 载板和 FPC 的规模占比低于全球市场,可见在附加值较高的 PCB 产品的生产技术及市场份额等方面,中国尚不及欧美日等发达国家。
随着技术的迭代和产品应用的升级,国内主要 PCB 厂商也不断向高阶产品进发,在HDI 板、IC 载板和 FPC等领域不断扩大产能,随着高阶 PCB 产品的持续布局,未来中国厂商将凭借成本、效率等优势逐步抢占高阶 PCB 的市场份额。
按照下游应用领域分布来看,根据世界电子电路理事会(WECC)数据,2022 年中国 PCB 行业下游应用领域中,通信、计算机、汽车电子和消费电子合计占比 87%,是最主要的四大应用市场。
在通信领域,PCB 主要运用于通信基站、传输设备、路由器、交换机、服务/存储设备等。2020 年是全球 5G 规模扩展元年,各国纷纷加快 5G 建设。5G对通信设备性能要求提升导致单体基站 PCB 量价齐升,以及 5G 基站的换建与新建,使得 PCB 在通信领域将迎来高速成长期。在计算机领域,PCB 主要运用在服务器/存储器、个人电脑及外部设备等设备中。
近年来,随着云计算、大数据等技术发展,互联网数据中心作为处理、存储、备份数据的重要物理载体快速发展,而云计算集中化和价格下降也倒逼互联网数据中心朝着大规模/超大规模发展,拉动了互联网数据中心的建设需求,同时带动了服务器和存储器的增长,使得计算机领域的 PCB 需求将大幅增加。
在汽车电子领域,PCB 主要运用于汽车电子控制装置(如发动机电子、底盘电子、驾驶辅助系统、车身电子)和车载电子装置(如娱乐系统)等。在智能驾驶和新能源汽车的驱动下,汽车电子单车配套价值的提升,汽车电子有望成为 PCB 发展的新动能。在消费电子领域,PCB 主要运用于手机、家电、可穿戴设备、无人机、VR/AR 设备等产品中。
消费电子种类多、更新快,叠加消费升级之大趋势,消费者逐渐从以往的物质型消费走向服务型、品质型消费。目前,消费电子行业正在酝酿下一个以人工智能、物联网、智能家居为代表的新蓝海,创新型消费电子产品层出不穷,并将渗透消费者生活的方方面面。
消费电子市场的快速增长也推动了 PCB 行业的发展。在工控医疗领域,PCB 主要运用于工业电脑、变频器、测量仪、医疗显示器等设备中。随着全球人口加速老龄化便携式医疗、家用医疗设备的需求急剧增长,使得医疗设备拥有广阔的发展前景。
随着电子技术的飞速发展,中国和全球 PCB 产业也在持续成长。根据Prismark 的数据,预计 2023-2028 年全球 PCB 产值在通信和消费电子领域的带动下将增长至 904.1 亿美元,复合增长率将达到 5.4%;中国 PCB 产值将增长至 464.7 亿美元,复合增长率将达到 4.2%。未来五年,中国和全球 PCB 市场将保持持续增长。
受益于全球 PCB 产能向中国转移以及下游蓬勃发展的电子终端产品制造的影响,中国已成为全球第一大 PCB 制造基地。根据 Prismark 预测,未来 5 年亚洲将继续主导全球 PCB 市场的发展,而中国在 PCB 行业的地位将更加稳固。
PCB 的下游终端应用领域广泛,包括通信、计算机、消费电子、汽车电子、工业控制和医疗、航空航天等。
广泛的终端应用分布为 PCB 行业提供巨大的市场空间,下游终端应用行业存量市场规模的稳定增长为 PCB 行业发展提供了基础,降低了行业发展的风险。同时,电子产业突飞猛进,下业技术不断革新,PCB 的下游终端应用市场呈现多元化趋势,产品的运用范围也大幅扩增,5G、Mini-LED、AR/VR、可折叠手机、新能源汽车等领域的蓬勃发展为 PCB行业带来了广阔的增量应用市场。
随着下游终端电子产品朝着高性能化、多功能化和信号传输高频(速)化的方向迅速发展,推动了 PCB 行业快速地从传统 PCB 走向以高集成化、高性能化为特点的高阶 PCB,具体体现如下:
(a)高系统集成化。智能终端的每次升级都会对产品的集成度和多功能化提出更高要求。以智能手机为例,在不断要求输入/输出端口数目增多、引脚间距减小、功能元件数增多的需求面前,PCB 产品设计日趋复杂,电路板上的集成密度不断提升。刚挠结合、埋入式元器件等小型化 PCB 产品能够提供更高密度的电路互连、容纳更多的电子元件,在多功能集成、体积重量减小等方面具有很大优势。全球主要 PCB 厂商均致力于在减小 PCB 产品体积与重量的同时附加更多的功能元件,这些要求对 PCB 电镀的精细度与信赖度提出更高的挑战。
(b)高性能化。高阶 PCB 产品未来将进入快速增长阶段,对数据传输频率及速度、数据容量的要求会更高。随着数字传输信号日益高频化,具备良好的阻抗性的 PCB 产品才能保障信息的有效传输。PCB 产品电路阻抗越低,其性能就越稳定,越可实现高频高速工作,从而承担更复杂的功能。PCB 产品高性能化的趋势也推动 PCB 的制作工艺向微孔化、细线化、多层化的方向发展。在此背景下,国内主要 PCB 厂商未来将致力于完善和扩充产品品类,不断提升高阶化 PCB 产品产能和产量。
凭借绿色、环保且成本持续下降等优势,近年来光伏行业处于快速发展阶段。为早日实现碳中和及碳达峰,我国政府积极推动光伏产业的健康发展,我国光伏新增装机量不断提升。根据中国光伏行业协会统计数据,2015 年我国光伏新增装机量为 15.1GWh,2022 年增长至 87.4GWh,年均复合增长率为 28.5%。
在我国光伏产业链成本日渐下降及产品技术持续提升的背景下,中国光伏行业协会预测,2023-2030 年我国年均新增光伏装机将达到 104-127GWh,全球光伏年均新增装机将达到 344-406GWh。
根据原材料和电池制备技术的不同,光伏电池可分为 P 型电池和 N 型电池。P 型硅片是在硅料中掺杂硼元素制成;N 型硅片是在硅材料中掺杂磷元素制成。2021 年后 N 型电池开始快速发展,其中以 TOPCon 和 HJT(异质结)两条路线为主导,两者现阶段处于大规模商业化的前期阶段。
TOPCon 和 HJT 电池技术理论光电转换效率超过 28%,具有非常大的市场潜力。根据中国光伏行业协会数据,2021 年全球光伏银浆消耗量约达 3,378 吨,耗银量占全球白银产量的 19%;2022 年我国光伏银浆消耗量预计 4,177 吨,同比增加 35.9%;浆料成本约占光伏电池成本的 10%~20%。
根据中国光伏行业协会《中国光伏产业发展路线 年)》,TOPCon 电池银浆消耗量约为 115mg/片,HJT 电池银浆消耗量约为 127mg/片,相比主流 PERC 技术银浆耗量 91mg/片,分别增加了 26.37%和 39.56%的银浆耗量。TOPCon、HJT 等 N 型电池技术的发展,光伏行业对银浆的耗用量会进一步增加。
电池片生产成本中的非硅材料具有很大的降本空间,其中,银浆的使用量大、价格高,银浆成本是非硅成本下降的关键。在不影响电池转化效率的前提下,可以减少贵金属银的使用量,利用价格较低的金属替代一部分银粉,从而达到降低成本的效果,具体操作方法包括铜电镀和银包铜。其中,铜电镀可实现铜替代银浆,并具有超细线宽、高可靠性、可量产性等优势。随着铜电镀等技术逐步成熟,光伏行业对铜球铜粉产品的需求将大大提升,铜球铜粉市场规模也将进一步扩大。
铜球是一种电镀材料,下游应用领域主要包括 PCB 制造、光伏电池板制造、五金电镀等,其中铜球实现的主要功能都是在铜电镀过程中作为阳极材料向镀液中补充铜离子。
铜球产品(以磷铜球为主)是铜电镀工序的主要物料,铜球的品质对镀层的品质和制造良品率具有重要的影响。随着技术的不断进步,主流阳极电镀铜材料完成了由从纯铜材料向添加了磷元素的磷铜合金材料转变,发展过程如下:
硫酸盐镀铜是应用最广泛的无氰镀铜工艺,具有成分简单,成本低,维护方便等优点,加入添加剂后,可直接获得光亮镀铜层,从而省去了机械抛光工序。
在 1954 年以前,硫酸盐镀铜工艺中采用的是纯铜作为阳极,由于电镀液中含有硫酸,使得纯铜阳极在电镀液中溶解很快,导致电镀液中的铜离子迅速累积,失去平衡。另一方面纯铜阳极在溶解时会产生少量一价铜离子(Cu+),它在电镀液中很不稳定,通过歧化反应分解成为二价铜离子(Cu2+)和微粒金属铜,在电镀过程中很容易在镀层上面成为毛刺。
为消除阳极Cu+的影响,人们最早使用阳极袋,但泥渣过多妨碍了电镀液的循环。后改用无氧高导电性铜阳极,虽然泥渣减少了,但仍不能阻止铜金属微粒的产生,于是又采用定期在电镀液中加入双氧水使Cu+氧化成Cu2+,但此法在化学反应中要消耗一部分硫酸,导致电镀液中的硫酸浓度下降,必须及时补充,同时又要补充被双氧水氧化而损耗的光亮剂,增加了电镀成本。
1954 年美国 Nevers等人对铜阳极的研究发现在铜阳极中渗入少量的磷,经过一定时间的电解处理后,铜阳极的表面生成一层黑色胶状的“磷膜”,它的主要成分是磷化铜(Cu3P,又称阳极膜),在电镀时阳极溶解几乎不产生铜粉,泥渣极少,零件表面铜镀层不会产生毛刺。这是由于含磷铜阳极的黑色膜具有导电性能,其孔隙又不影响铜离子自由通过,加快了 Cu+的氧化,阻止了 Cu+的积累,大大地减少了电镀液中 Cu+;同时又使阳极的溶解与阴极沉积的效率渐趋接近,保持了镀铜液中铜含量平衡。
美国福特汽车公司使用这种含磷铜阳极的经验证明既保证了镀铜层质量,又大幅降低了电镀光亮剂的消耗,降低了成本。从此以后,含磷铜阳极在酸性镀铜行业中被广泛采用,随后又逐渐被 PCB行业大规模使用。
含磷铜阳极这一成果为硫酸盐光亮镀铜工艺的发展做出了重大贡献。在电镀的生产过程中,“磷”的加入有两个功能:一是为了抑制Cu+的产生;二是阻止 Cu+进入溶液,促使它进一步被氧化成Cu2+。“磷”在理论上亦为杂质,在满足以上两个功能的基础上,添加得越少越好。早期,由于设备差、技术水平不高,搅拌难以充分,不能保证磷分布均匀,只好采取加大磷含量的措施,通常将磷含量控制在 0.1%~0.3%。到二十世纪 70~80 年代,国外采用电解铜(或无氧铜)和磷铜合金为原料,用中频电炉熔炼,磷含量容易控制,逐渐形成了含磷量为 0.035%~0.070%的标准。
电子信息行业逐渐向精密化、集成化发展,要求铜球的晶粒尺寸要细小均匀,同时磷含量分布均匀,以保证阳极膜均匀,从而实现在相同电流和酸性环境条件下,Cu2+的电离以及结合均匀,形成均一的镀膜。下业的发展和技术进步推动了铜球行业生产工艺不断改进,技术标准不断提高,产品向微晶化、低磷化的方向发展。
目前,PCB 制造是铜球的最主要应用领域,也是对铜球产品技术要求最高的领域,PCB 行业较为成熟,公开的行业数据较为多,以 PCB 行业相关数据计算 PCB 制造用铜球市场空间如下:根据 Prismark 数据,铜球约占 PCB 成本的6%;2023 年全球 PCB 产值为 695.17 亿美元,国内 PCB 产值为 377.94 亿美元。
据此测算,2023 年全球铜球市场规模约为人民币 235.14 亿元,国内铜球市场规模约人民币 127.84 亿元。未来,随着终端应用的不断加深以及行业整体规模的提升,铜球产品的市场规模亦会不断增长。
印刷电路板,即 Printed Circuit Board,简称 PCB,是一种重要的电子器件,是电子元器件的支撑体,也是电子元器件电气相互连接的载体。PCB 是组装电子零件用的关键互连件,不仅为电子元器件提供电气连接,也承载着电子设备数字及模拟信号传输、电源供给和射频微波信号发射与接收等功能,绝大多数电子设备及产品均需配备,因而 PCB 也被称为“电子产品之母”,被广泛运用于通信、计算机、消费电子、汽车电子、工业控制和医疗、航空航天等行业。
PCB 的制造品质不仅直接影响电子产品的可靠性,而且影响芯片与芯片之间信号传输的完整性,其产业的发展水平可在一定程度上反映一个国家或地区电子信息产业的发展速度与技术水平。
PCB 上游生产原材料主要包括覆铜板(CCL)、铜箔、铜球/氧化铜粉、油墨、金盐及其他化工材料。其中,铜球(一般采用磷铜球)主要在 PCB 电镀工序中作为阳极氧化,参与化学反应,铜球约占 PCB 成本的 6%。PCB 应用范围广泛,下游应用涵盖通信、计算机、消费电子、汽车电子、工业控制和医疗、航空航天等领域。
随着电子技术的提升及电子产品的快速更迭,全球 PCB 产业呈现持续增长的发展趋势。根据 Prismark 数据,2022 年度全球 PCB 产值达到 817.4 亿美元,2010-2022 年,全球 PCB 产值复合增长率达到 3.8%。预计 2028 年全球 PCB 产值在通信和消费电子领域的带动下将增长至 904.1 亿美元,2023-2028 年复合增长率为 5.4%。全球 PCB 行业市场需求将进一步扩大,各大 PCB 制造商未来的扩产计划及设备换新需求将极大推动 PCB 产业链的不断进步和发展。
根据 Prismark 及公开资料,全球 PCB 行业于过去几十年中经历了多次产业格局变化。二十世纪 80 年代,美国作为全球 PCB 技术的主导国家,其 PCB 产值占全球总产值比例超过 30%;90 年代后,日本企业突破了 PCB 制造技术,超越美国成为新的制造中心;2000 年之后,中国台湾 PCB 市场迅速崛起,而欧美国家及日本迫于成本压力则相应收缩其 PCB 产值;自 2005 年以来,中国大陆依靠较低的综合成本、庞大的市场需求、逐步完善的配套资源等优势,成功超越日本并于当年首次成为全球最大 PCB 生产制造中心。
中国大陆 PCB 产值全球占比逐步由 2000 年的 8.1%,增加至 2008 年的 31.0%,进而增加至 2022 年的 53.3%。PCB 产业格局东移明显,过去二十多年来中国大陆 PCB 产值全球占比不断提升,预计未来几年仍将保持领先,占据世界核心地位。从 PCB 行业的发展来看,中国大陆虽然已经成为世界第一的 PCB 生产大国,但附加值较高的 PCB 产品的生产技术及市场份额,仍被欧美日等发达国家占据。
日本目前为全球最大的高附加值 PCB 生产地区,产品以多层板、HDI 板、IC 载板、FPC 为主;美国同样维持了高附加值 PCB 的研发及生产职能,产品以高阶、多层板为主,主要应用领域包括通信、医疗、航空航天、军工等领域。
从 PCB 产品结构情况来看,PCB 市场刚性板仍占主流地位,其中多层板是全球 PCB 行业中产值最大的产品;伴随 5G 基站、数据中心和网络技术设施设备、消费电子类可穿戴设备、IoT 市场等下游领域的快速发展,HDI 板、IC 载板及 FPC 等高附加值的 PCB 产品呈现迅速增长态势,预计未来几年也将保持较高的发展增速。
据 Prismark 预计,2023 年 HDI 线 亿美元,受库存改善和对汽车、高速光模块(400G、800G)、卫星通信和人工智能边缘设备的需求扩大的推动,全球 HDI 线 年 CAGR 将达 7.1%。
2023 年全球 IC 封装基板市场规模达 125.0 亿美元,受 FCBGA 用于高级 2.5 和 3D 封装领域、新兴的 AiP 和 SiP 基板及 FCCSP和存储器基板的持续增长等因素影响,预计 2028 年全球 IC 封装基板市场规模将达 190.7 亿美元,2023-2028 年 CAGR 达到 8.8%。两者年均复合增长率均超过行业整体增幅。
现阶段,高端 HDI 材料及封装基板材料主要集中于中国台湾、日本、韩国企业。随着国内厂商技术创新并进入核心供应链,预计未来几年中国大陆地区企业在 HDI 和 IC 载板材料的行业产值占比将大幅提升。
按照下游应用领域分布来看,根据 Prismark 的统计数据,2022 年度,计算机和通信为 PCB 的主要应用市场,应用占比分别为 33%和 32%。其次为消费电子、汽车电子领域,应用占比分别为 14%和 12%。其它领域,如工控医疗、军事/航空航天等应用占比相对较低。
我国 PCB 行业的整体发展趋势与全球 PCB 行业基本相同。受益于 PCB 行业产能不断向我国转移,加之通信、计算机、消费电子、汽车电子、工业控制和医疗、航空航天等下游领域的需求增长刺激,近年来我国 PCB 行业增速整体高于全球 PCB 行业增速。
根据 Prismark 数据,中国作为全世界最大的 PCB 生产基地,2022 年度 PCB 产值达到 435.5 亿美元,2010-2022 年,中国 PCB 产值复合增长率达到 6.6%,增速超过全球增速平均水平;预计 2028 年中国 PCB 产值将增长至 464.7 亿美元,2023-2028 年复合增长率将达到 4.2%。中国 PCB 市场目前发展势态平稳,预计未来增速将与全球增速基本持平。
中国已形成了较为成熟的电子信息产业链,同时具备内需市场广阔、人力成本较低、投资环境良好等优势,吸引了大量外资企业将生产重心向中国大陆转移。珠三角地区、长三角地区由于下游产业集中,并具备良好的区位条件,成为了我国 PCB 生产的核心区域。但近年来,随着沿海地区制造成本上升,部分 PCB 企业开始将产能向中西部地区迁移,尤其是江西、湖北、重庆等经济产
业带的 PCB 产能呈现快速增长的发展势头。江西省作为沿海地区向中部延伸的重要地带,兼具独特的地理位置及丰富的资源优势,加上地方政府大力支持电子信息产业发展,逐渐成为沿海地区 PCB 企业主要转移基地。预计未来珠三角地区、长三角地区仍将保持 PCB 产业的领先地位,并不断向高端产品和高附加值产品方向发展;中西部地区由于 PCB 企业的内迁,逐渐成为中国 PCB 行业的重要生产基地。
随着全球产业规模的不断扩张,中国区域的 PCB 产业也呈现持续升级的发展形态趋势,高阶多层板、FPC、HDI 板等产品的产能均得到一定提升。
PCB 细分产品中,多层板产值占比最高,其次是单/双面板、HDI 板和 FPC,IC 载板占比稳步提升。和全球 PCB 市场产品结构对比来看,中国市场的单/双面板和多层板的规模占比高于全球市场,而 IC 载板和 FPC 的规模占比低于全球市场,可见在附加值较高的 PCB 产品的生产技术及市场占有率等方面,中国尚不及欧美日等发达国家。
随着技术的迭代和产品应用的升级,国内主要 PCB 厂商也不断向高阶产品进发,在HDI 板、IC 载板和 FPC等领域逐步扩大产能,随着高阶 PCB 产品的持续布局,未来中国厂商将凭借成本、效率等优势逐步抢占高阶 PCB 的市场份额。
按照下游应用领域分布来看,根据世界电子电路理事会(WECC)数据,2022 年中国 PCB 行业下游应用领域中,通信、计算机、汽车电子和消费电子合计占比 87%,是最主要的四大应用市场。
在通信领域,PCB 主要运用于通信基站、传输设备、路由器、交换机、服务/存储设备等。2020 年是全球 5G 规模扩展元年,各国纷纷加快 5G 建设。5G对通信设施性能要求提升导致单体基站 PCB 量价齐升,以及 5G 基站的换建与新建,使得 PCB 在通信领域将迎来高速成长期。在计算机领域,PCB 主要运用在服务器/存储器、个人电脑及外部设备等设备中。
近年来,随着云计算、大数据等技术发展,互联网数据中心作为处理、存储、备份数据的重要物理载体加快速度进行发展,而云计算集中化和价格下降也倒逼互联网数据中心朝着大规模/超大规模发展,拉动了互联网数据中心的建设需求,同时带动了服务器和存储器的增长,使得计算机领域的 PCB 需求将大幅增加。
在汽车电子领域,PCB 主要运用于汽车电子控制装置(如发动机电子、底盘电子、驾驶辅助系统、车身电子)和车载电子装置(如娱乐系统)等。在智能驾驶和新能源汽车的驱动下,汽车电子单车配套价值的提升,汽车电子有望成为 PCB 发展的新动能。在消费电子领域,PCB 主要运用于手机、家电、可穿戴设备、无人机、VR/AR 设备等产品中。
消费电子种类多、更新快,叠加消费升级之大趋势,消费者逐渐从以往的物质型消费走向服务型、品质型消费。目前,消费电子行业正在酝酿下一个以AI、物联网、智能家居为代表的新蓝海,创新型消费电子科技类产品层出不穷,并将渗透消费者生活的方方面面。
消费电子市场的迅速增加也推动了 PCB 行业的发展。在工控医疗领域,PCB 主要运用于工业电脑、变频器、测量仪、医疗显示器等设备中。随着全球人口加速老龄化便携式医疗、家用医疗设施的需求急剧增长,使得医疗设施拥有广阔的发展前景。
随着电子技术的快速的提升,中国和全球 PCB 产业也在持续成长。根据Prismark 的数据,预计 2023-2028 年全球 PCB 产值在通信和消费电子领域的带动下将增长至 904.1 亿美元,复合增长率将达到 5.4%;中国 PCB 产值将增长至 464.7 亿美元,复合增长率将达到 4.2%。未来五年,中国和全球 PCB 市场将保持持续增长。
受益于全球 PCB 产能向中国转移以及下游蒸蒸日上的电子终端产品制造的影响,中国已成为全世界第一大 PCB 制造基地。根据 Prismark 预测,未来 5 年亚洲将继续主导全球 PCB 市场的发展,而中国在 PCB 行业的地位将更加稳固。
PCB 的下游终端应用领域广泛,包括通信、计算机、消费电子、汽车电子、工业控制和医疗、航空航天等。
广泛的终端应用分布为 PCB 行业提供巨大的市场空间,下游终端应用行业存量市场规模的稳定增长为 PCB 行业发展提供了基础,降低了行业发展的风险。同时,电子产业突飞猛进,下业技术不断革新,PCB 的下游终端应用市场呈现多元化趋势,产品的运用范围也大幅扩增,5G、Mini-LED、AR/VR、可折叠手机、新能源汽车等领域的蓬勃发展为 PCB行业带来了广阔的增量应用市场。
随着下游终端电子科技类产品朝着高性能化、多功能化和信号传输高频(速)化的方向快速地发展,推动了 PCB 行业快速地从传统 PCB 走向以高集成化、高性能化为特点的高阶 PCB,具体体现如下:
(a)高系统集成化。智能终端的每次升级都会对产品的集成度和多功能化提出更加高的要求。以智能手机为例,在不断要求输入/输出端口数目增多、引脚间距减小、功能元件数增多的需求面前,PCB 产品设计日趋复杂,电路板上的集成密度不断的提高。刚挠结合、埋入式元器件等小型化 PCB 产品可提供更高密度的电路互连、容纳更多的电子元件,在多功能集成、体积重量减小等方面具有很大优势。全球主要 PCB 厂商均致力于在减小 PCB 产品体积与重量的同时附加更多的功能元件,这些要求对 PCB 电镀的精细度与信赖度提出更高的挑战。
(b)高性能化。高阶 PCB 产品未来将进入迅速增加阶段,对数据传输频率及速度、数据容量的要求会更高。随着数字传输信号日益高频化,具备良好的阻抗性的 PCB 产品才能保障信息的有效传输。PCB 产品电路阻抗越低,其性能就越稳定,越可实现高频高速工作,从而承担更复杂的功能。PCB 产品高性能化的趋势也推动 PCB 的制作流程与工艺向微孔化、细线化、多层化的方向发展。在此背景下,国内主要 PCB 厂商未来将致力于完善和扩充产品品类,不断的提高高阶化 PCB 产品产能和产量。
凭借绿色、环保且成本持续下降等优势,近年来光伏行业处于快速发展阶段。为早日实现碳中和及碳达峰,我国政府积极推动光伏产业的健康发展,我国光伏新增装机量不断的提高。根据中国光伏行业协会统计数据,2015 年我国光伏新增装机量为 15.1GWh,2022 年增长至 87.4GWh,年均复合增长率为 28.5%。
在我国光伏产业链成本日渐下降及产品技术持续提升的背景下,中国光伏行业协会预测,2023-2030 年我国年均新增光伏装机将达到 104-127GWh,全球光伏年均新增装机将达到 344-406GWh。
根据原材料和电池制备技术的不同,光伏电池可分为 P 型电池和 N 型电池。P 型硅片是在硅料中掺杂硼元素制成;N 型硅片是在硅材料中掺杂磷元素制成。2021 年后 N 型电池开始加快速度进行发展,其中以 TOPCon 和 HJT(异质结)两条路线为主导,两者现阶段处于大规模商业化的前期阶段。
TOPCon 和 HJT 电池技术理论光电转换效率超过 28%,有很大的市场潜力。根据中国光伏行业协会数据,2021 年全球光伏银浆消耗量约达 3,378 吨,耗银量占全球白银产量的 19%;2022 年我国光伏银浆消耗量预计 4,177 吨,同比增加 35.9%;浆料成本约占光伏电池成本的 10%~20%。
根据中国光伏行业协会《中国光伏产业高质量发展路线 年)》,TOPCon 电池银浆消耗量约为 115mg/片,HJT 电池银浆消耗量约为 127mg/片,相比主流 PERC 技术银浆耗量 91mg/片,分别增加了 26.37%和 39.56%的银浆耗量。TOPCon、HJT 等 N 型电池技术的发展,光伏行业对银浆的耗用量会促进增加。
电池片生产所带来的成本中的非硅材料具备很大的降本空间,其中,银浆的使用量大、价格高,银浆成本是非硅成本下降的关键。在不影响电池转化效率的前提下,能够大大减少贵金属银的使用量,利用价格较低的金属替代一部分银粉,进而达到减少相关成本的效果,具体操作方法有铜电镀和银包铜。其中,铜电镀可实现铜替代银浆,并具有超细线宽、高可靠性、可量产性等优势。随着铜电镀等技术逐步成熟,光伏行业对铜球铜粉产品的需求将极大的提升,铜球铜粉市场规模也将进一步扩大。
- 其他产品